Specialist Sewing Machine Servicing in Liverpool
Sewing machines play an essential role in delivering an effective Design & Technology (DT) education. They offer students practical, hands-on experience that helps them to develop their skills and build confidence – but only if they’re in good working order. If your sewing machines aren’t properly serviced, they can disrupt lessons, delay projects, and even pose a health risk.
To guarantee a safe and stimulating learning environment, you need reliable and efficient sewing machine servicing from DCE. Our experts have helped schools and commercial businesses across the North West to keep their equipment running smoothly and avoid costly downtime. Get in touch to find out how we can help.
Contact Us
"*" indicates required fields
Expert sewing machine servicing for all major brands
At DCE, we’re committed to providing a comprehensive and reliable sewing machine maintenance and repairs service. Our expert technicians are highly experienced in tackling a full range of sewing machines from leading manufacturers.
As a result, we can offer a service that’s fully tailored to the specific needs of your school or business, ensuring that all of your sewing machines operate safely and effectively in even the most demanding circumstances.
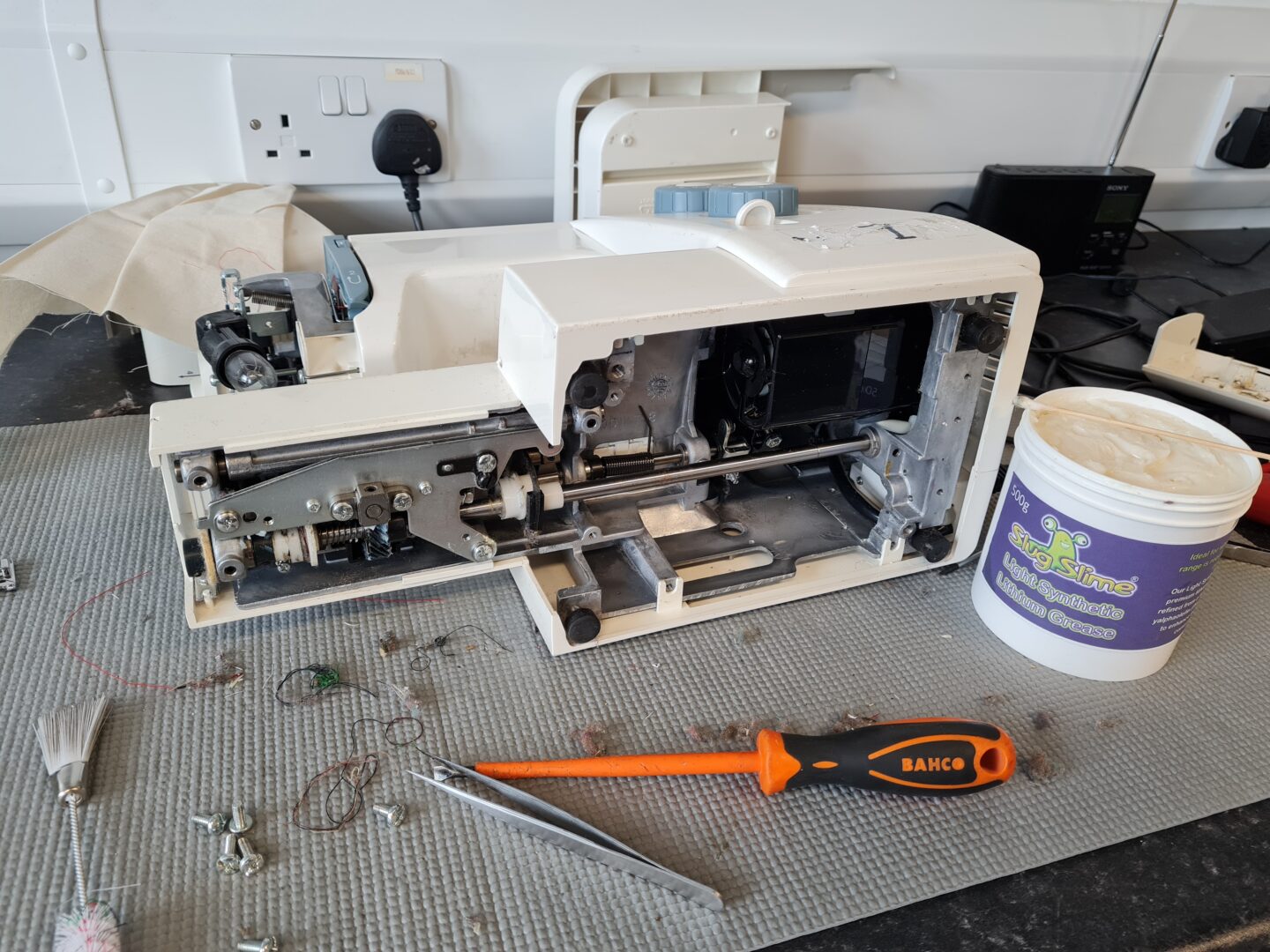
We are approved dealers for a range of industry-leading brands including:
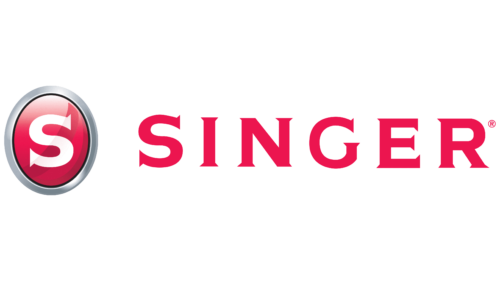
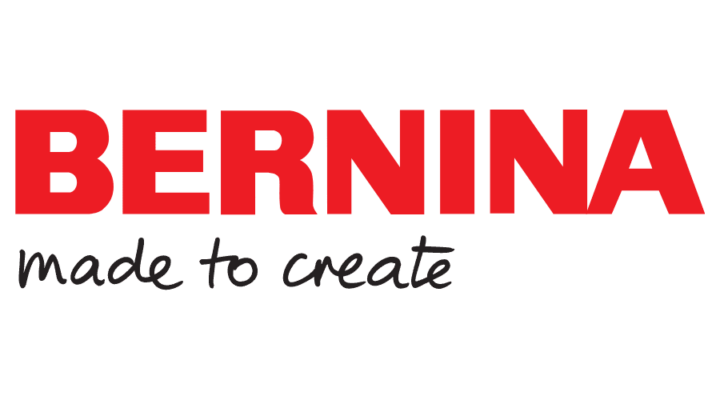
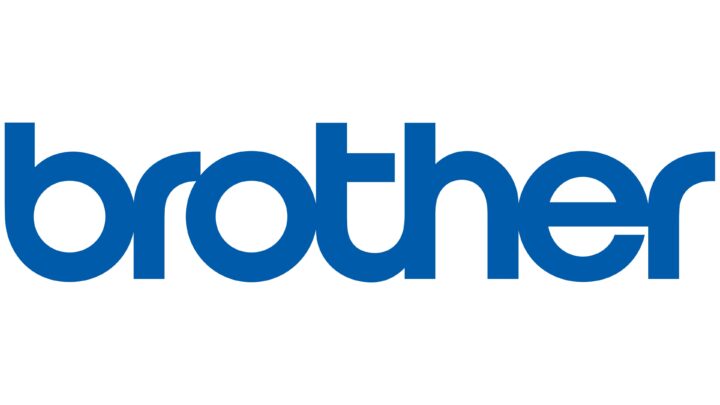
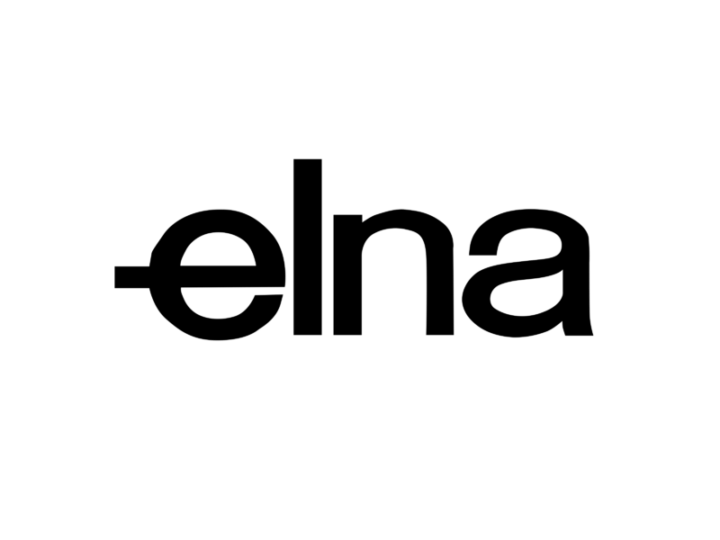
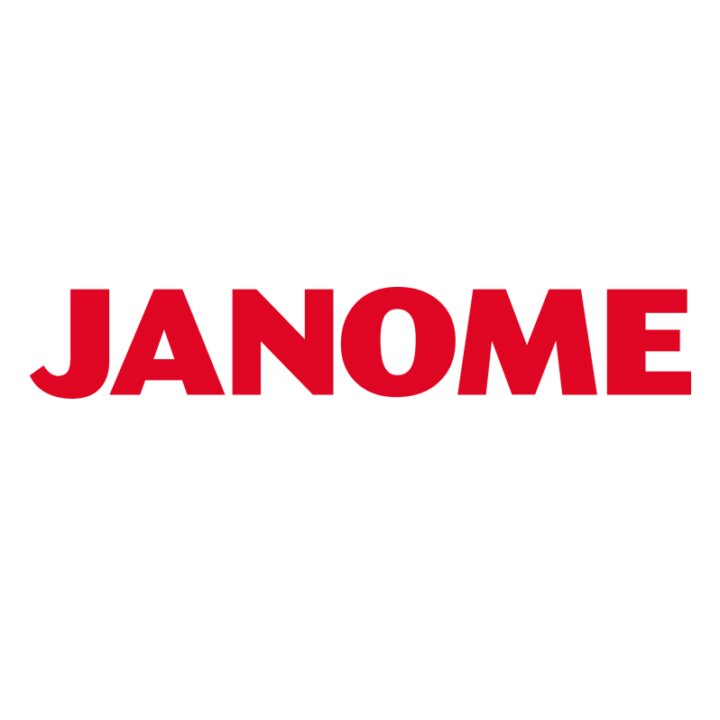
A trusted on-site service for schools and businesses
Keeping your sewing machines in top condition is vital – but it’s just as important that regular servicing doesn’t interrupt your lessons or slow your business down. At DCE, we offer a sewing machine maintenance service that fits with your schedule without taking shortcuts on safety.
Our fully DBS-checked technicians will arrive on-site in full uniform with ID badges and provide in-depth servicing of all your sewing machines. From external and internal checks to cleaning and PAT testing, we’ll ensure your sewing machines are working at their best, giving you the peace of mind you need to continue delivering classes with confidence
Our Sewing Machine Servicing Process
Initial consultation. From your first enquiry, we develop a full understanding of your needs, including the number and type of sewing machines you have and any specific issues you’re facing.
Full sewing machine servicing. Our technicians arrive on site in full uniform with ID badges to deliver an in-depth servicing for all your sewing machines and any other DT equipment that requires attention.
Scheduling remedial work. If your sewing machines require any remedial work or emergency repairs, we can quote for this and schedule it in to suit your needs.
Full reporting. We provide detailed reports to give you a full overview of any tests performed and work carried out.
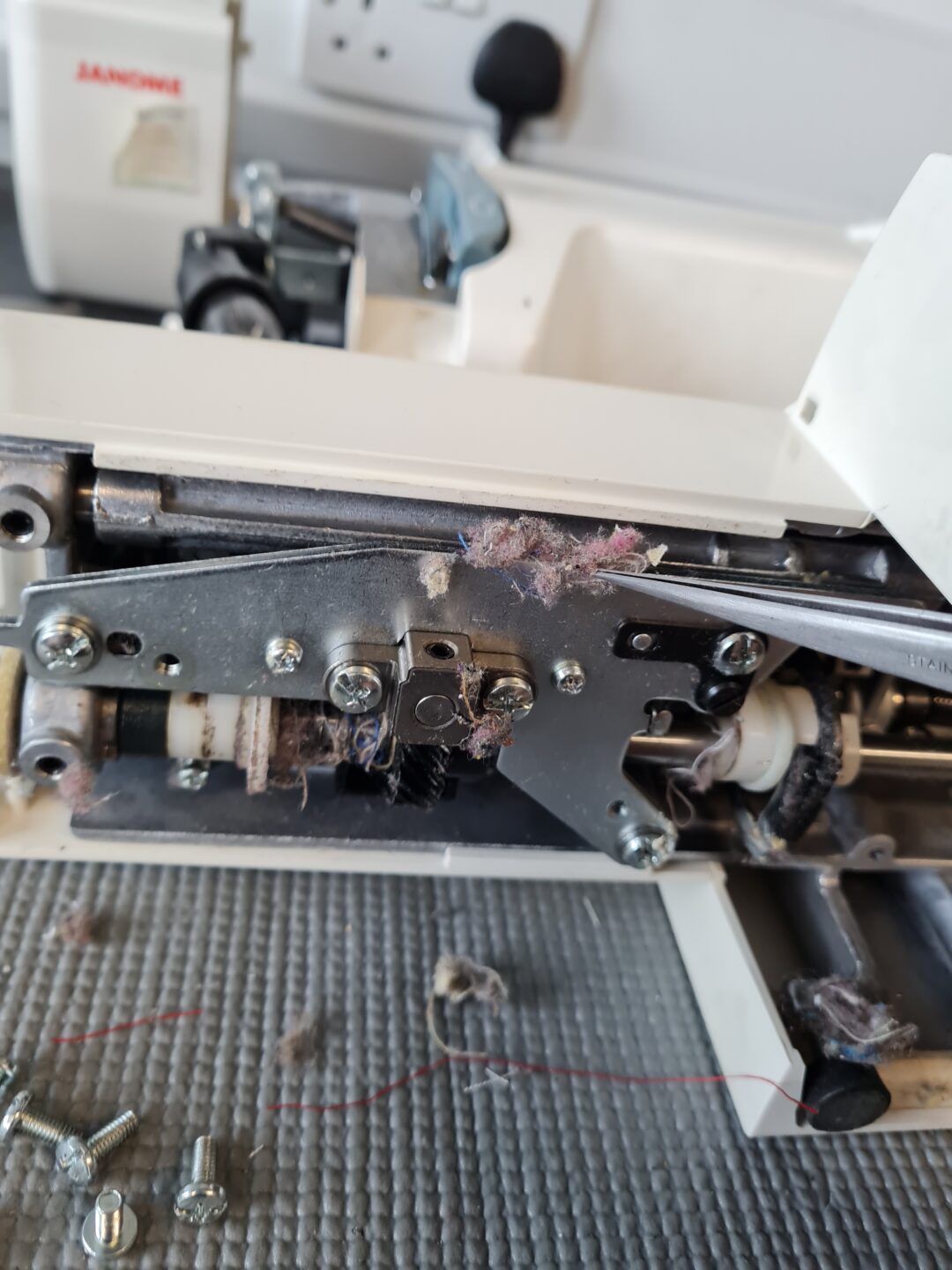
Full range of DT equipment services
At DCE, we’re not just sewing machine specialists – we can provide a comprehensive, expert-led planned preventative maintenance (PPM) and repairs service for all your DT equipment. From bandsaws and bench drills to pottery kilns and beyond, we can help to protect your essential equipment and ensure you can deliver a safe, reliable and effective educational experience.
In addition to servicing and repairing a full range of DT equipment, we also offer a fully certified and compliant LEV COSHH testing service. We can ensure your DT workshop and science fume cupboard extractor systems are working optimally and keeping staff and students safe from hazardous substances.
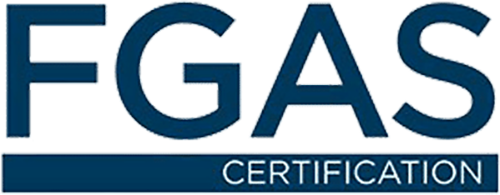
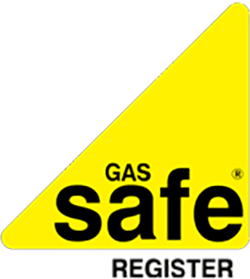
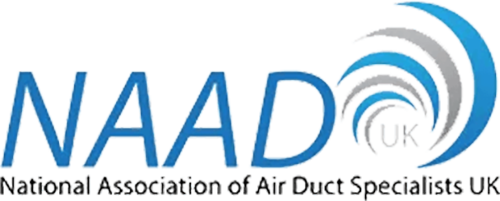
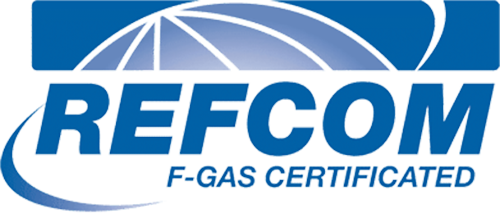
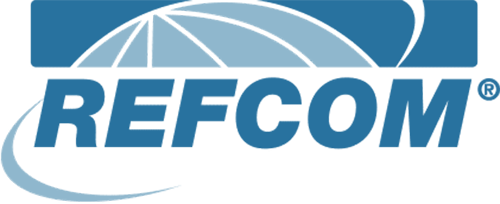
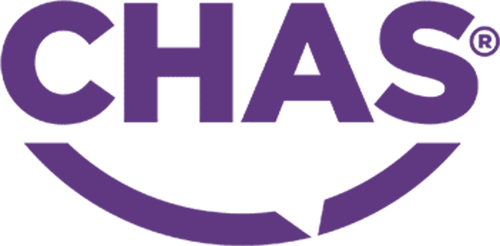
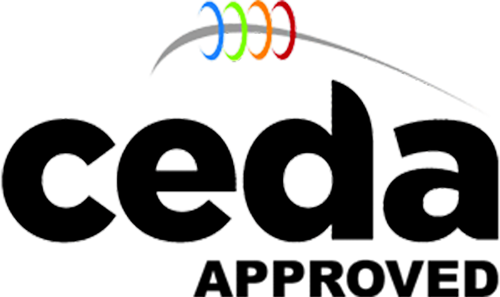
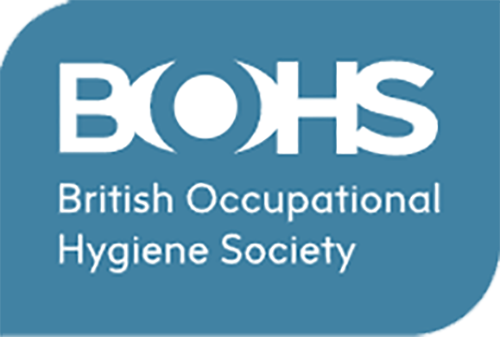
Frequently Asked Questions
Why do sewing machines need servicing?
Sewing machines are sensitive instruments with many moving parts. Coupled with the kind of intensive usage they are often exposed to in schools and commercial businesses, this can lead to a range of common issues. From bobbin tension slippages to inconsistent stitching, your sewing machines can quickly become ineffective – or even unsafe – for use in lessons, leading to prolonged downtime and project delays.
Regular servicing is the most effective way to limit these kinds of issues and minimise disruption to your school or business. With experienced technicians examining and testing your sewing machines at regular intervals, you’ll be able to catch any emerging issues early and fix them before they lead to costly breakdowns. Servicing can also help to limit wear and tear, saving you money on repairs and replacements over the long-term.
How often should sewing machines be serviced?
For school environments, where sewing machines see frequent use by students who may not have mastered the proper technique, we recommend servicing them every 6 to 12 months. This ensures that the machines remain in optimal working condition, preventing issues caused by wear and tear from heavy use by students.
In a commercial setting with even higher usage, more frequent servicing may be required, depending on the intensity of use. Regular servicing helps catch any emerging problems early, reducing the risk of breakdowns and costly repairs.
How much does sewing machine servicing cost?
The cost of sewing machine servicing can vary depending on the type and number of machines, the condition they’re in, and any specific repairs that may be needed. To provide an accurate estimate, we recommend getting in touch with us for a full consultation. A member of our expert team will be in touch to discuss your situation and offer a tailored quote based on your school or business’s specific requirements.
What does a typical sewing machine service include?
At DCE, we are committed to delivering a comprehensive, in-depth and reliable sewing machine maintenance service. Our technicians will provide:
- External appliance checks including examining the foot control, handwheel, clutch and bobbin winder, the needle alignment and the external casing.
- Internal checks if faults are suspected, including looking for tension and wear on the drive belt and examining the operation of the internal bearings and gears.
- Cleaning the machine and lubricating it, alongside removing lint and any old oil.
- Portable Appliance Testing (PAT) to ensure your sewing machines are running safely and there are no underlying electrical issues.
With the results of our inspection in hand, you can be confident that your sewing machines aren’t just safe to use, but that they’re also performing at their very best. You can focus on delivering your classes without having to worry about unexpected issues.
Can you provide remedial repairs for sewing machines?
Yes, if our technicians identify any issues during the maintenance service, they can diagnose the problem and provide a quote for repairs. If you’re happy with the quote, we can get your sewing machine back in working order again as soon as possible. And with an extensive van stock of common parts, our technicians can often provide repairs right then and there, minimising any disruption to your services.
Do you provide reports as part of your sewing machine servicing?
Yes, we provide you with a detailed, in-depth report for every single sewing machine we service. This will break down the results of the tests we’ve performed and summarise our assessment, including whether any repairs are required. All reports are signed and dated by the technician that performed them, giving you full transparency.